กระบวนการผลิตบรรจุภัณฑ์แก้ว
แบ่งออกได้เป็น 9 ขั้นตอนง่ายๆ คือ
1. การเตรียมวัตถุดิบ (Raw Material Preparation)
เริ่มตั้งแต่การตรวจรับ และตรวจสอบคุณภาพของวัตถุดิบชนิดต่างๆ ตามมาตรฐาน เมื่อวัตถุดิบผ่านการตรวจสอบคุณภาพแล้ว จะถูกจัดเก็บไว้ในคอกเก็บ และถังพักต่างๆ แยกตามชนิดของวัตถุดิบ
2. การชั่งตวงวัตถุดิบ (Weighing)
วัตถุดิบชนิดต่างๆ ซึ่งเก็บไว้ในไซโลในโรงผสมวัตถุดิบจะถูกนำมาชั่งน้ำหนักให้ได้ค่าตามที่กำหนดไว้ในสูตรผสมของแต่ละสีแก้ว ซึ่งจะมีค่าแตกต่างกัน ทั้งเรื่องชนิดของวัตถุดิบและค่าน้ำหนัก การชั่งน้ำหนักของวัตถุดิบจะกระทำครั้งละ จำนวน 1 โม่หรือ แบช (Batch) ต่อเนื่องกันไปจนได้ปริมาณสำรองตามที่ต้องการ ทั้งนี้ในกระบวนการชั่งวัตถุดิบจะใช้คอมพิวเตอร์ควบคุม
3. การผสมวัตถุดิบ (Mixing)
วัตถุดิบที่ผ่านการชั่งน้ำหนักแล้วจะถูกส่งเข้าโม่ผสม (Mixer) เพื่อที่จะทำให้เกิดการคลุกเคล้าเข้ากัน วัตถุดิบที่ผสมเข้ากันดีแล้ว เรียกว่า ”ส่วนผสม” (Batch) จะถูกลำเลียงพร้อมด้วยเศษแก้ว (Cullet) เพื่อส่งไปเก็บยังไซโลของเตาหลอม และรอการป้อนเข้าเตาหลอมต่อไป
4. การหลอม (Melting)
วัตถุดิบจะถูกป้อนอย่างต่อเนื่องเข้าไปในเตาหลอม ซึ่งความร้อนในการหลอมแก้วจะได้โดยการใช้ก๊าซธรรมชาติและกระแสไฟฟ้า วัตถุดิบจะถูกหลอมเหลวที่อุณหภูมิในเตาหลอมประมาณ 1,500 องศาเซลเซียส และที่สภาวะนี้ฟองแก๊สที่เกิดขึ้นจากปฏิกิริยาการหลอม ไม่ว่าจะเป็น CO2 และ SO3 จะค่อยๆ ระเหยออกไปจากผิวแก้ว และออกไปจากเตาหลอมผ่านทางปล่อง ซึ่งจะทำให้น้ำแก้วมีความพร้อมที่จะทำการขึ้นรูปได้ดี
5. การขึ้นรูป (Forming)
น้ำแก้วที่ได้จากการหลอมเหลวจะถูกส่งจากเตาหลอมผ่านรางลำเลียงไปยังสายการผลิต น้ำแก้วจะถูกตัดเป็นก้อนแก้ว (gob) ให้มีขนาด รูปร่างและอุณหภูมิที่เหมาะสมและจะต้องให้ได้น้ำหนักของก้อนแก้วเท่ากับขวดแก้วที่ต้องการด้วย ต่อจากนั้น gob จะถูกปล่อยให้หยดลงไปในแบลงค์ (blank) หรือเบ้าชุดแรกเพื่อขึ้นรูปขั้นต้นที่เรียกว่า พาริสัน (parison) ซึ่งจะมีปากที่สมบูรณ์และรูปทรงที่พอเหมาะ เตรียมส่งไปยังอีกเบ้าหนึ่งที่เรียกว่าโมลด์ (mould) หรือเบ้าพิมพ์สำหรับขึ้นรูปลำตัวและก้นให้เป็นบรรจุภัณฑ์แก้วที่เสร็จสมบูรณ์ กระบวนการขึ้นรูปบรรจุภัณฑ์แก้วที่ใช้กันอยู่ปัจจุบันแบ่งเป็น 3 แบบ หลักๆได้แก่
• Blow & Blow (B&B) เป็นการขึ้นรูป parison ด้วยการใช้ลมแรงสูงเป่าอัดน้ำแก้วให้เป็นรูปทรงตามแบบเบ้าปากและเบ้า blank และส่งไปยัง mould เพื่อเป่าอีกครั้งให้ได้รูปร่างสุดท้ายของบรรจุภัณฑ์ที่ต้องการ วิธีนี้ใช้กับบรรจุภัณฑ์ปากแคบ เช่น ขวดเบียร์ ขวดเหล้า ขวดน้ำอัดลม เป็นต้น
• Press & Blow (P&B) ต่างจาก B&B ตรงที่การขึ้นรูป parison จะใช้เดือยอัดน้ำแก้วให้ได้รูปร่างตามแบบเบ้าปากและเบ้า blank แล้วส่งไปยัง mould โดยใช้เทคนิคการเป่าเหมือนกัน วิธีนี้ใช้กับบรรจุภัณฑ์ขวดปากกว้าง เช่น ขวดบรรจุอาหาร ขวดเครื่องดื่มซุปไก่ เป็นต้น
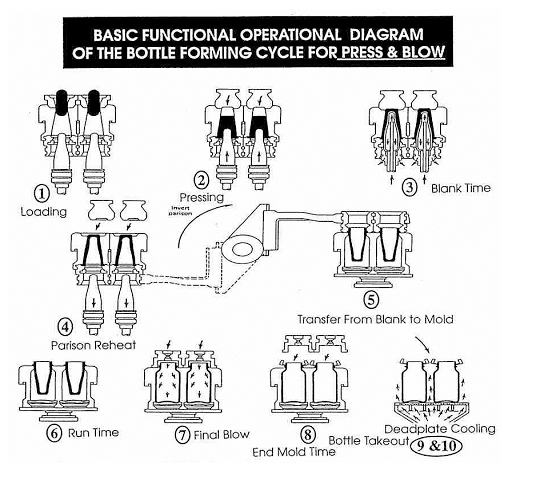
• Narrow Neck Press & Blow (NNPB) คล้ายกับ P&B เพียงแต่ขนาดของปากที่จะขึ้นรูปสำหรับกระบวนการนี้จะแคบ เนื่องจากบรรจุภัณฑ์ที่ขึ้นรูปด้วยกระบวนการนี้จะมีน้ำหนักเบา และมีความบาง ดังนั้นจึงเหมาะกับบรรจุภัณฑ์ประเภทที่ใช้ครั้งเดียว (One Way)
ในขั้นตอนการขึ้นรูปนี้ พนักงานควบคุมเครื่องจักรขึ้นรูปจะดูแลตรวจสอบคุณภาพในการผลิต ไม่ว่าจะเป็นน้ำหนักขวด รูปทรงสัณฐานของขวด หรือรอยตำหนิต่างๆ ที่กำหนดไว้ในมาตรฐานการผลิต เพื่อให้มั่นใจว่าได้ผลผลิตที่ดีก่อนส่งผ่านไปยังกระบวนการถัดไป
6. การอบ (Annealing)
บรรจุภัณฑ์แก้วที่ขึ้นรูปแล้วจะถูกลำเลียงมาตามสายพานลำเลียงเข้าไปยังรางอบ (Annealing Lehr) เพื่อปรับลดอุณหภูมิลงอย่างช้าๆจากประมาณ 550 องศาเซลเซียส ให้ค่อยๆ เย็นลงจนถึงอุณหภูมิปกติ หลังจากนั้นบรรจุภัณฑ์แก้วทุกใบจะถูกเคลือบด้วยน้ำยา Cold-end spray เพื่อให้ผิวด้านนอกมีความลื่น เรียบสวยงาม และไม่เป็นรอยเมื่อเสียดสีกัน
7. การตรวจสอบและการประกันคุณภาพ
• 100% Machine inspection
หลังจากเคลือบน้ำยาแล้วบรรจุภัณฑ์แก้วทุกใบจะต้องผ่านเครื่องตรวจคุณภาพอัตโนมัติ เพื่อที่จะทำการตรวจหาความบกพร่อง (Defects) ต่างๆตั้งแต่ ปาก ลำตัว ไปจนถึงบริเวณก้น บรรจุภัณฑ์ที่ได้มาตรฐานจะถูกส่งไปบรรจุในขั้นตอนถัดไป ส่วนบรรจุภัณฑ์ที่ไม่ได้มาตรฐาน จะถูกนำกลับไปหลอมใหม่
• Quality Assurance – Lab tester
นอกจากนั้นแล้ว TGI ยังมีแผนกประกันคุณภาพ ที่จะทำหน้าที่เสริมความมั่นใจด้านคุณภาพโดยจะสุ่มตรวจสินค้าที่บรรจุพร้อมส่งไปให้ลูกค้าตามมาตรฐานการสุ่มตรวจที่ถูกกำหนดไว้ เพื่อความมั่นใจว่าสินค้าที่ออกจากโรงงานมีคุณภาพได้มาตรฐาน การตรวจสอบบรรจุภัณฑ์แก้วในห้องแลบ ถือเป็นการประกันคุณภาพอีกส่วนหนึ่ง โดยจะตรวจวัดคุณลักษณะต่างๆทางด้านฟิสิกส์ ไม่ว่าจะเป็น ความหนา ขนาด น้ำหนัก การทนต่อแรงกระแทก อุณหภูมิที่แตกต่าง (Thermal Shock) ความสามารถในการทนต่อแรงอัดและสารเคมี ถ้าสินค้าที่ผลิตในลอตนั้นได้มาตรฐานก็จะถูกส่งไปจำหน่ายยังลูกค้า หากไม่ผ่านมาตรฐาน ก็จะถูกกักไว้เพื่อนำไปตรวจสอบอย่างละเอียดต่อไป
8. การพิมพ์สี
บรรจุภัณฑ์บางชนิด โดยเฉพาะอย่างยิ่งบรรจุภัณฑ์สำหรับบรรจุเครื่องดื่มและน้ำอัดลมต้องมีการพิมพ์สีเพื่อแสดงตรายี่ห้อผลิตภัณฑ์ บรรจุภัณฑ์ที่ผ่านการตรวจสอบคุณภาพแล้วจะถูกส่งมายังส่วนงานพิมพ์สีซึ่งใช้เทคนิคการพิมพ์ซิลค์สกรีน (Silkscreen printing) ลงบนพื้นผิวบรรจุภัณฑ์ หลังจากนั้นบรรจุภัณฑ์แก้วที่พิมพ์สีแล้วจะถูกนำไปเข้ารางอบที่มีอุณหภูมิสูงถึง 600 องศาเซลเซียส เพื่อให้สีที่พิมพ์ติดอยู่บนพื้นผิวถาวร
9. การบรรจุ (Packing)
บรรจุภัณฑ์แก้วที่ผ่านการผลิตและตรวจสอบทุกขั้นตอนจนแน่ใจว่าได้คุณภาพตรงตามความต้องการของลูกค้าแล้วจะถูกบรรจุด้วยเครื่องบรรจุอัตโนมัติ (Palletizer) จากนั้นจะมีการพันฟิล์มหรือคลุมถุงครอบกระบะไว้ให้เรียบร้อย ก่อนที่จะนำไปเก็บไว้ในคลังสินค้ารอการจัดส่งต่อไปยังลูกค้า