Production of glass containers.
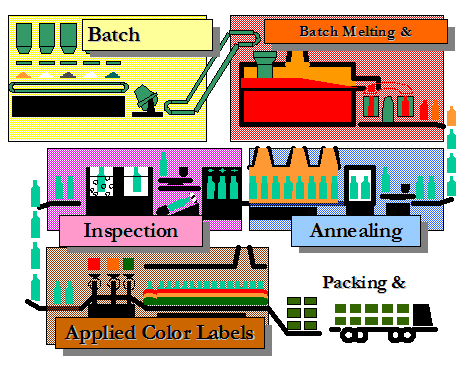
1. Incoming raw material inspection and storage: raw materials arrive at glass container plants are sampled and inspected according to their specifications. Once passed the inspection, they will be stored properly for subsequent uses.
2. Weighing and mixing: each raw material is weighed according to a batch recipe using a computerized system and will be transferred to a mixer. Mixed raw material or batch will be stored in a silo and ready to be loaded into a furnace. Batch is continuously fed into the glass furnace operated using natural gas, oil and electricity. Batch is generally melted at 1,500 degrees Celsius and at this state gas bubbles such as CO2 and SO3 generated by melting reactions slowly evaporate away from the molten glass surface. Refined molten glass delivered through working end and forehearth is then ready for forming operation.
3. Forming: At the end of forehearth, molten glass is cut into a lump of glass called gob to proper size, shape and temperature as needed by forming operation. Gob is then delivered into a blank side to form an initial shape called parison. At this stage, complete bottle finish is formed. Parison is inverted into a mould side to form a complete bottle shape. According to modern glass container manufacturing, there are three common forming processes as following.
3.1 Blow & Blow (BB): in this process, parison and bottle cavity are formed by compressed air. This technique is used for manufacturing narrow mouthed glass containers such as soft drink, beer and liquor bottles.
3.2 Press & Blow (PB): in this process, only parison cavity is formed using a plunger. Final cavity on the mould side is formed by compressed air as in the BB technique. This technique is used for manufacturing wide mouthed containers such as food jars, chicken essence bottles and coffee jars.
3.3 Narrow Neck Press & Blow (NNPB): this technique is similar to the PB technique. The plunger used in this process is generally long compared to the BB process. Precise parison cavity and glass distribution is easily obtained at this stage. Parison is subsequently blown to form a final bottle cavity with better glass distribution compared to the BB technique. This technique is used to manufacture modern lightweight and non-returnable narrow mouthed containers.
Bottles obtained from the forming machine are carefully monitored and inspected for weight, shape and appearance defects by forming staffs to ensure that minimum defective bottles will enter to the next process.
4. Annealing: hot glass containers from the forming machines will be transported down the conveyor into the annealing Lehr. The purpose of this process is to slowly decrease bottles temperature to minimize residual stress in containers. Residual stress in containers can result in immediate breakage or weakening of containers strength for subsequent uses. Containers exiting the annealing lehr are also sprayed on outer surface to improve surface finish and durability of glass containers.
5. Inspection and Quality Assurance.
5.1 Automatic finish product inspection: all containers from the annealing lehr are physically screened by series of automatic finish product inspecting machines. Appearance defects and inclusions are detected throughout a container. Defective bottles are then automatically rejected for remelting process.
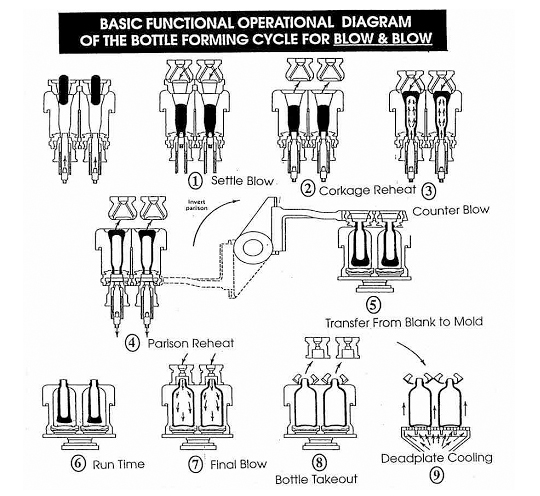
5.2 Quality Assurance - Lab testers: besides automatic inspecting machines, glass containers are sampled and tested for other properties such as thermal shock, hydrostatic pressure and impact resistances. Glass containers with unsatisfactory test results will be quarantined for repeating test or scraping. This is to insure that the quality of every glass container is satisfactory and meet customer satisfaction.
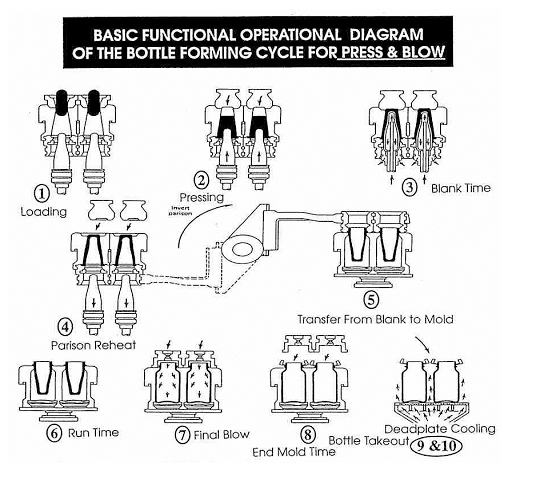
6. Labeling and decoration: upon requests from customers, label and decoration can be applied to glass containers using applied ceramic labeling (ACL) technique. Ceramic colors are applied to glass containers and heat treated at the temperature approximately 600 degrees Celsius.
7. Packing: glass containers ready for delivery to customers will be palletized and shrink wrapped using automatic machines. Glass container pellets are stored in well managed and hygienic warehouse and ready to be delivered to customers.